Mechanical drives are used to transmit motion, torque and power from driver shaft (usually a prime mover like electric motor) to driven shaft (such as machine unit). There are four mechanical drives, namely gear drive, belt drive, chain drive and rope drive. Each of them has specific features and is suitable for certain type of applications. A gear drive is preferred for power transmission over small distance. It is one positive drive and can be designed to transmit power at any angle and any plane. There are four basis types of gears—spur gear, helical gear, bevel gear and worm gear. A spur gear has straight teeth parallel to the gear axis and can transmit power between parallel shafts only. However, due to sudden contact between teeth of two mating spur gears, tooth experiences shock or impact loading.
Problems associated with impact loading can be eliminated by utilizing helical gear. Like spur gear, helical gear is also used for parallel shafts; however, teeth are cut in the form of helix on the cylindrical gear blank. The helical teeth of two mating gears gradually come in contact, resulting a gradual loading on the teeth (instead of impact loading as in case of spur gear). This also increases power transmission capability and at the same time reduces vibration. However, helical profile of the tooth induces axial thrust load on the bearing, which is sometimes detrimental and limits the maximum allowable speed of application. In order to eliminate the thrust force maintaining the helical form of teeth intact, either herringbone gear or double helical gear can be employed.
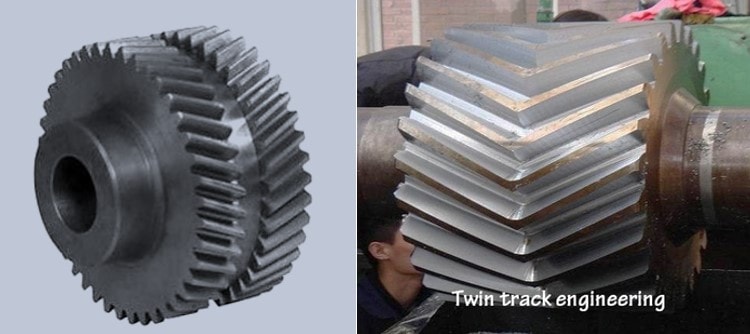
In both the cases, teeth are cut in two halves of the gear blank maintaining same module, number of teeth and helix angle but opposite hand of helix. Thus thrust force produces by each half of the gear is equal and opposite and thus eliminates each other. Although herringbone gear or double helical gear is free from axial load, there are few differences between them in terms of constructional feature and their manufacturing. In double helical gear, small relief gap is provided between two halves. So teeth of left hand helix do not physically touch the teeth of right hand helix. However, in case of herringbone gear, no such gap is provided and thus teeth having left hand helix touch the teeth having right hand helix. Various differences between herringbone gear and double helical gear are given below in table format.
Table: Difference between herringbone gear and double helical gear
Herringbone Gear | Double Helical Gear |
---|---|
In herringbone gear, no gap is provided between two halves. So teeth with left hand helix touches the teeth with right hand helix. | In double helical gear, small relief gap is provided between two halves. So teeth with left hand helix do not touch the teeth with right hand helix. |
Its manufacturing is difficult and requires dedicated machine. | Its manufacturing is comparatively easy as it can be cut by hobbing, shaping or even milling. |
It has less axial length and thus can be used where space is limited. | Other features being same, it requires more axial space due to presence of relief gap. |
Presence of relief gap: A relief gap between the left hand helix teeth and right hand helix teeth is the main differentiating factor. In herringbone gear, no gap is provided and thus left hand helix teeth remain in physical contact with right hand helix teeth. In double helical gear, a small gap (2 – 10cm based on size) is maintained between left hand helix teeth and right hand helix teeth.
Difficulty in manufacturing the gears: While cutting the gear teeth for herringbone gear, the cutter is not allowed to move beyond the teeth face in one side (where junction exists). Any overstepping will create undesired groove on other half as intermediate groove or space does not exist. This makes the manufacturing complicated and a dedicated machine is required to cut such gear teeth. In case of double helical gear, the small relief gap allows the cutter to move freely beyond the teeth face. Due to difficulty in manufacturing, cost of herringbone gear is marginally higher than the cost of similar double helical gear.
Axial width: Width or thickness of the gear actually determines tooth strength and power transmission capability. Due to presence of small relief gap in double helical gear, tooth face width is not equivalent to the gear width. For same gear width and other features, teeth face width of herringbone gear will be larger and consequently its transmission capability will be higher. Inversely, for specified power transmission, a thinner herringbone gear can be employed. This is particularly suitable for designing a compact machine unit having limited available space.
Scientific comparison among herringbone gear and double helical gear is presented in this article. The author also suggests you to go through the following references for better understanding of the topic.
- Design of Machine Elements by V. B. Bhandari (Fourth edition; McGraw Hill Education).
- Machine Design by R. L. Norton (Fifth edition; Pearson Education).
- A Textbook of Machine Design by R. S. Khurmi and J. K. Gupta (S. Chand; 2014).